GEA – Training Excellence with VR
Manufacturing Industry
Enhancing Skills with VR Training for
Rotary Atomizer F100 Operators
ABOUT
About GEA
The company GEA is currently a global leader in the field of engineering for process industries and they specialize in providing cutting edge solutions for diverse sectors such as food, beverages, pharmaceuticals and more. The company was established in 1881 and they design and implement solutions for different industrial processes and their focus is to maximize efficiency and minimize environmental impact.
They operations in over 60 countries and their expertise spans a wide range of industries, offering technologies and industries that help companies enhance their productivity while also ensuring quality and meeting environmental standards. GEA is a trusted partner for any businesses that seek new and innovative process solutions whether it is advanced machinery for dairy production or industrial heating and cooling solutions for climate friendly production.
GEA embraced digital transformation by integrating advanced technologies like Virtual Reality (VR) into their operations. These initiatives help with the optimization of manufacturing and training processes and they also position them as a frontrunner in the industry. GEA continues to set the standard for excellence in industrial engineering through its commitment to innovation and customer centric solutions.
Challenge
With over 2,000 serviceable machines in operation at the moment and an average cost of €5,000 per trainee, GEA has identified a challenge in their current approach to training their new workforces. Given the large scale of GEA’s operations, their new employees come from different regions or countries, which means that travel expenses such as flights, accommodations, meals, and transportation quickly add up. It is both costly and time consuming to coordinate travel for new trainees especially because it depends on the geographical spread of their workforce. As such, travel times could be long, resulting in extended training schedules that increase overall expenses.
In order to overcome this and reduce travel costs while delivering high quality training, GEA is exploring the potential of VR technology. Virtual reality would allow them to reduce the need for travel which allows for more frequent and flexible training sessions and offers a consistent and scalable training solution.
VR Immersive Solution
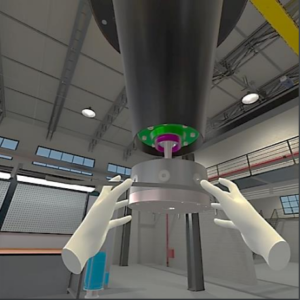
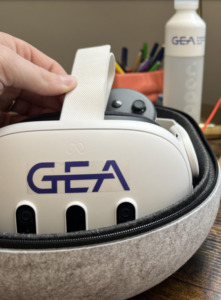
Recreate created a complete training from A – Z on the overhaul of a Rotary Atomizer F100!
To address challenges in training technicians for the maintenance and overhaul of the Rotary Atomizer F100, a hands-on, immersive training program was developed. This program covers the entire process, including maintenance, disassembly, assembly, and familiarization with the machine. It offers a guided and assisted learning experience with built in skill verification to ensure comprehensive understanding.
The initiative aims to:
- Train technicians more efficiently, at a reduced cost per learner, and in a sustainable manner using immersive technologies.
- Formulate data security and compliance strategies.
- Develop an effective content management strategy for training materials.
- Measure training outcomes to evaluate the program’s success.
Key Achievements
- Enhanced Engineering Quality: A highly accurate CAD model of the F100 was developed, serving as a quality benchmark for engineering processes.
- Evaluation and Alignment: An evaluation strategy was implemented to measure training success, alongside stronger alignment between engineering and technical departments.
- Innovation Milestone: This project represents the most advanced digital training solution developed in LPT.
The program successfully completed its first training, involving two technicians. Moreover, feedback highlighted significant interest and enthusiasm for immersive technologies across other teams and departments.
This immersive training solution demonstrates the potential to completely transform technical education within the company. With further adoption, it could pave the way for increased operational efficiency, enhanced technician expertise, and expanded use cases in other areas.
Discover our Projects in
Manufacturing