Cutting Construction Failure Costs by 50% with Mixed Reality
The construction industry is a complex ecosystem where precision, efficiency, and quality are paramount. However, it is also an industry plagued by high failure costs, which recent research suggests can amount to over 12% of the total project cost. These costs, often hidden, represent a significant drain on resources and profitability.
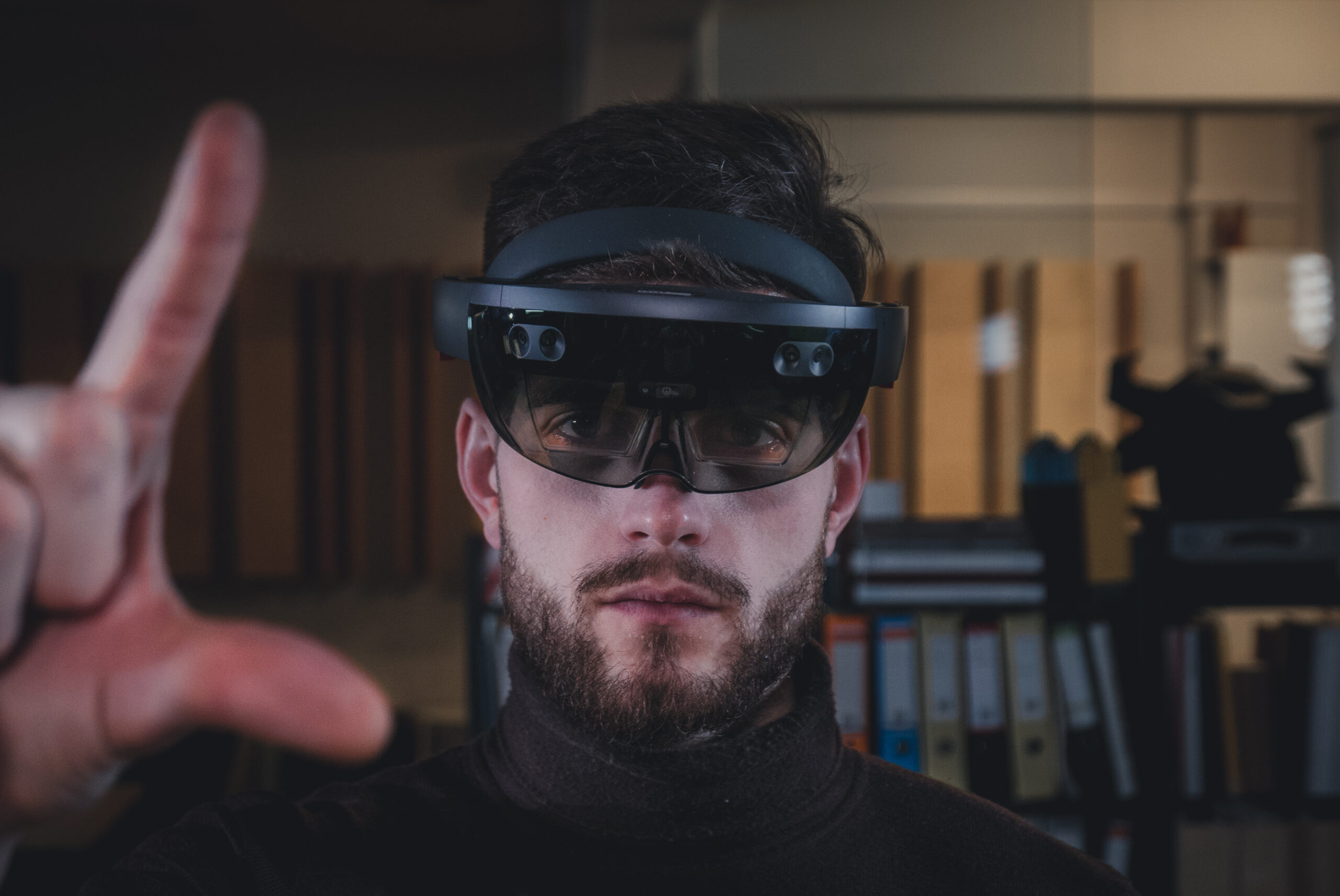
This article explores how Mixed Reality (MR) and Augmented Reality (AR) technologies can help reduce these failure costs, particularly for manufacturing companies supplying custom-made products like steel beams and concrete floors for the construction industry.
The High Cost of Failure
Failure costs in the construction industry are a significant concern. They represent the financial impact of correcting errors and inefficiencies that occur throughout a project’s lifecycle. According to a report by ABN Amro, these costs can be substantial, often exceeding the industry’s total annual profit. The primary contributors to these costs are inefficient management practices and a lack of quality control during the manufacturing and assembly process.
The Promise of Mixed Reality and Augmented Reality
MR and AR technologies offer a promising solution to these challenges. By overlaying digital information onto the physical world, these technologies can provide real-time, contextual data that enhances understanding and decision-making. For manufacturers of custom-made construction products, MR and AR can be particularly beneficial in ensuring quality control. For example, these technologies can be used to verify the measurements of custom-made steel beams and concrete floors, ensuring they meet project-specific requirements.
Importance of Measurement and Quality Control
In the construction industry, accurate measurements are crucial. A slight deviation from the specified dimensions can lead to significant problems, including structural instability and increased failure costs. This is where MR and AR technologies come into play. They allow for precise measurements in real-time, ensuring that the manufactured products meet the exact specifications. This not only reduces the chances of errors but also eliminates the need for costly rework, thereby saving both time and money.
Business case
Conclusion
The adoption of MR and AR technologies in the construction industry presents a compelling business case. Not only can these technologies significantly reduce failure costs, but they can also enhance efficiency, improve quality control, and ultimately boost profitability. For CFOs, COOs, and Heads of Engineering looking to drive innovation and value in their organizations, investing in MR and AR technologies could be worthwile investigating.